Learn
Learning Center
This page will contain information all about plasma cutting for those who are new to it. This section is under construction, please come back soon.
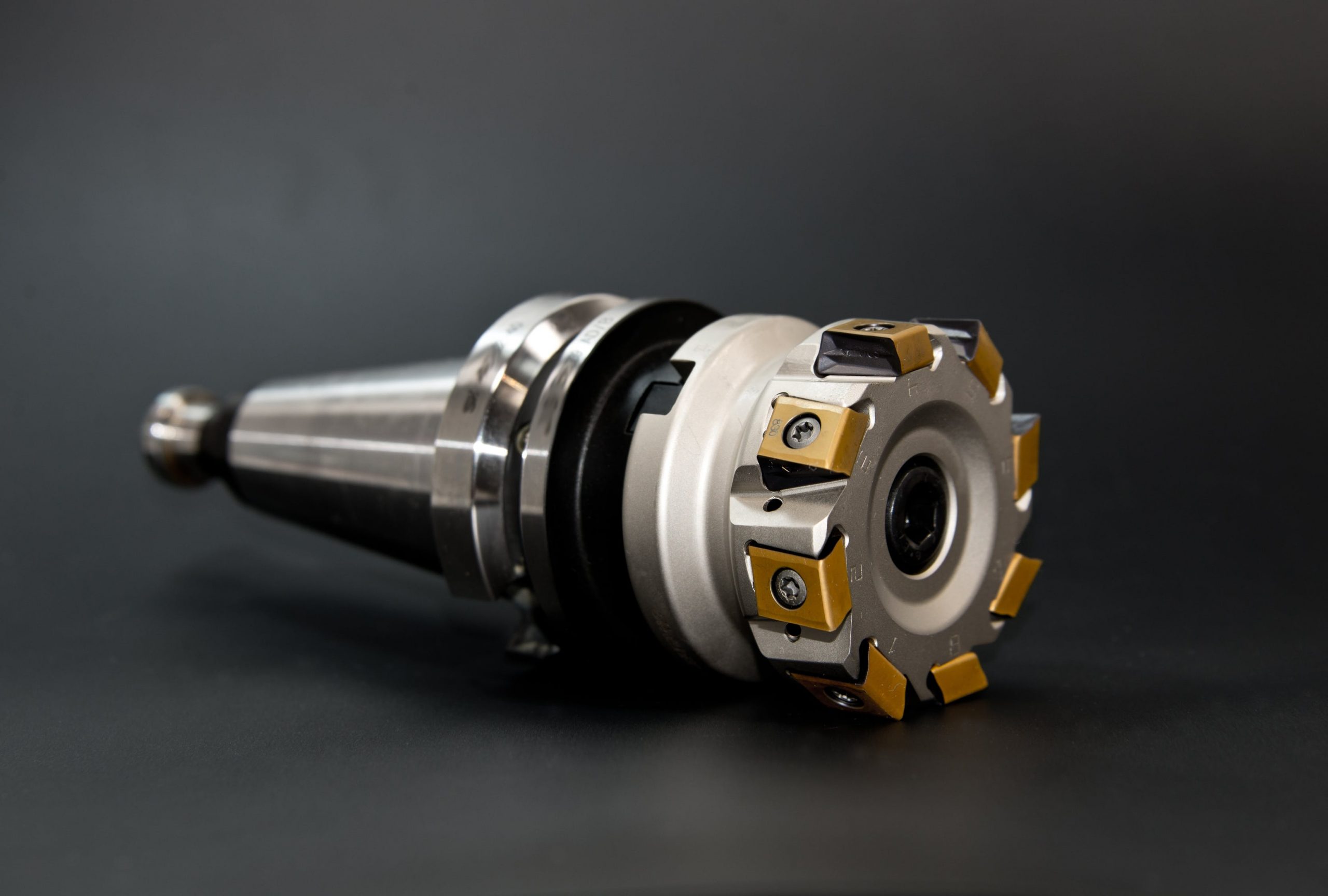
Plasma 101
CNC plasma cutting, like many other disciplines, has unique attributes and methods. We hope to give a new user some basics as an introduction to this fascinating and useful subject.
A plasma cutting machine typically takes ordinary compressed shop air, strips off its electrons converting it to a super hot ionized state (plasma). A hand held or machine operated torch projects the super hot plasma against the material to be cut. When the plasma hits the material it melts; the melted material is blown away by the force of the moving plasma leaving a hole or gap. By moving the torch across the material, a continuous gap is created much like one created by a saw blade. A hand held torch is limited in accuracy by the hand that holds it. A machine torch is a specialized torch designed to be held and moved by a computer controlled gantry system, which assures accuracy in complex cutting operations.
There are two types of CNC plasma cutting systems: Standard and High Definition. High Definition systems utilize the same ionized gas principle but different torch design and gas feeds. High Definition can produce cleaner, more precise cuts than standard plasma cutting systems but generally cost as much as $30,000. For the purpose of this discussion, we will stick to Standard plasma cutting at a small fraction of High Definition costs.
What can you do with a CNC Plasma Cutting Machine? Essentially, you can cut simple or complex shapes into any material that can conduct electricity. Typical materials would be common steels and aluminum. Non-typical materials might include brass or copper titanium (creates toxic fumes) with special provision for venting, vision protection and gas selection. Complex shapes can be cut into flat stock, tubing, angles etc. Cutting can be done rapidly, accurately and with repetition. Cutting parts for mechanical assemblies or artwork of great complexity can be accomplished with equal speed and accuracy.
Can you cut watch gears with a CNC plasma cutter? No, and you can’t engrave on diamonds either. The gas-like plasma removes material while it cuts much like a saw blade cutting a board. Like any device that removes material while cutting, plasma cutters have limitations on doing very small detailed work. However, small work without tiny inside radiuses is well within its capabilities. Additionally, formerly tedious tasks like locating a pattern of holes can be done through a series of pierces for later drilling to finished size. This can save many hours of layout work. We have cut a number of ¾” by ¾” parts with a located hole in the center many times. Because of its low cost and high versatility, plasma cutting has become a fabrication tool in thousands of shops.
How does an object go from a drawing to finished part? First there is software. CNC plasma cutting requires three basic types of software: creation, conversion/modification and execution.
Creation software actually generates the drawing that will be cut. Parts for fabricated assemblies are created by CAD packages like AutoCAD, ProgeCad, Enroute 6, Solid Works and many others. These CAD systems have a universal export (interchange) format called DXF. Drawings produced in a DXF format can be easily imported into most plasma cutting systems. DXF drawings are in a vector format as opposed to a raster format. Vectors are lines of specific length and direction. Raster formatted drawings are made up of a series of dots. Bitmaps and “Gif” drawings would be examples of raster images. Although the human eye can interpret raster images, a CNC machine cannot. Raster images must be converted to vector format. There are many ways to do this. Some methods are good, some bad. You can call us for a further discussion of this subject. AutoCAD, Turbo CAD, Corel, Photo Shop and dozens of others can provide you assistance in creating drawings suitable for importing into your plasma cutting system. Since excellent drawing creation software is available on the open market, we leave it up to the user to select what is best for their unique needs. If you need some help in that direction? Call us. We are anxious to help.
As mentioned, the plasma cutter removes material while cutting. The width of the cut, as an example, might be .040. If we center the cut on the parts edge, we will remove .020 off the part’s edge. This will produce an undersized part. If we offset the cut .020 into the waste side of the material the part will be properly cut. Specified offsets can be created in most good CAD packages.
At the start of each cut the plasma cutter makes an initial round pierce. From the pierce hole the CNC plasma cutter begins cutting its normal slot. If we were cutting out a box-shaped object and began with a pierce at one corner. The round pierce hole would nip off the corner a bit and leave that corner poorly formed. To prevent this, we pierce the material a short distance away from the object, start the cut and proceed into the object with a fully established, clean cutting arc. The cut from the pierce point to the beginning of the object is called a “lead in” (see figure 1). Similarly we want to terminate the arc away from the object, so we continue the arc a short distance beyond the normal completion point. This is called a: lead out.”
CNC machines move according to very specific instructions given to them. These instructions are in the form of a CNC machine programming language. This programming language is called G and M coding. Since the typical drawing input format is a DXF file we need some way to convert it to G/M code. Some CAD software can save a drawing directly in a G Code format skipping the need to convert a DXF file. As part of its structure Our software provides a simple means of converting DXF files into G Code.
In addition to doing a G-Code conversion our software does much more. Typically a DXF drawing file generated by a CAD package needs a bit of “tuning up” to optimize it for CNC cutting. For example, a drawing may need to be joined. Picture a drawing of a box. The box may consist of four separate lines at right angles, or, it may consist of one line with four right angles. This is a big difference. The CNC Plasma cutter will interpret the separate line box as needing four independent cuts and will stop and restart at each corner. This will produce a sloppy part. The CNC cutter will cut the one line box differently. It will start at one corner and cut all around the box without stopping till it returns to where it started, which results in a much better part. Our software allows you to take separate lines, arcs, etc. and join them into one line entity for optimum cutting.
A drawing may need to be sequenced. Imagine you want to cut a donut. If you cut the outside circle first, the part will drop out of the material stock and you will not have the opportunity to cut out the center hole. When a CAD program creates a drawing, the order the drawing parts were created in is the order they will be cut. In most cases the order they were created in will not be the order you want them to be cut. Our software allows you to reorder the cut sequence to your choices.
Once you are satisfied that your drawing is properly joined and sequenced, the software should be able to save it as a G-Code file. When the G-Code is created you have completed all the work needed on the drawing file and it is ready to cut.
The execution portion of the software will then process the G-Code into the drive components and cut your parts.
At this point we should discuss the steps involved in plasma cutting.
In the first step the torch needs to properly locate itself above the material. That the torch must be over the proper location to begin the first cut is obvious. What may not be as obvious is that the torch must also be the proper distance above the work. To do this the torch must locate the material in relation to itself. There are three basic types of material sensors the torch can use to “find” its initial height above the material. The three sensors are: a mechanical switch, proximity and pressure sensing. The torch positions itself over the starting point, lowers itself, finds the material using one of the three sensing methods, then raises itself to an optimal height for an initial material pierce. Do not confuse the pierce height and cutting height. The pierce height is larger than the cutting height. When piercing there is a momentary molten material splash. You want the torch tip high enough to avoid the splash fouling the torch tip, but close enough to make a clean pierce. Once the material is pierced and arc established the torch should lower itself to an optimal cutting height.
Maintaining the proper gap distance between the torch tip and material wile cutting is critical. Anyone stating otherwise is being less than honest with you. Material as received from the mill is not perfectly flat. Material that may be reasonably flat will bow somewhat while it is being cut from heat warpage. If the material to torch tip distance is not maintained within a few thousandths of an inch, regardless of the material’s flatness, the cut will be poor and torch tips will not last. Maintaining the proper distance is the job of an automated torch height controller. Without an automated torch height controller there is NO way to maintain proper cutting (arc) gap. Again, some type of automated torch height controller is essential from day one. The best types maintain cutting gap by monitoring arc voltage. The best types can set an initial pierce height and maintain a separate cutting gap distance. Of course, our torch height controller can do both exceedingly well.
The plasma cutting arc produces an angular cut called a kerf. This means the cut edge may not be perfectly perpendicular. The thicker the material that is cut the more pronounced the kerf angle appears. Kerf angularity can be minimized by keeping in mind this rule of thumb. Using our donut as an example, cut the outside circle in a clockwise direction. Cut the inside circle in a counter clockwise direction.
While a cut is being made some of the oxidized material removed by the plasma arc is not completely blown away. It sticks to the cut edge in droplet form. This material is called dross or slag. Dross is very brittle and is easily removed by tapping it with a small hammer, grinding or sanding it off. The amount of dross produced is a function of cut speed, torch tip condition, material cleanliness and material quality.